Natural stone demand is increasing among property owners across the world. The use of different natural stone products is expanding and even changing with innovation. But not every natural stone installation turns out perfect.
Granite and marble suppliers need to comply with a number of factors to ensure each product matches the space it is made for. It is also important to work according to customer requirements, their design taste, and the specifications of the application. All of these potential challenges have only one solution. And that is a thorough quality inspection and quality assurance process.
Be it granite tile or marble tiles, for instance, each quarried stone is unique. The quality of the stone sourced for a particular project plays an instrumental role. It decides how the stone will look and perform after the finished installation. It also determines how it will look and perform ten years later.
Quality Marble Exports (India)
takes into account all of the above factors before delivering the final product for every project. We are sharing one such project’s quality inspection and assurance process journey which was accomplished in 2018.
Steps Involved Until The Product Delivery
1. Beginning Quality At The Quarry
Being a large-scale project, we chose a location in our quarry with immense mining capabilities that satisfy exact project specifications. This ensured that we get consistent, uniform, fresh, variation free, crack-free, fissure-less and six sides dressed dimensional stone blocks. We implemented the latest mechanical mining methods that adhere to environment-friendly quarrying practice with minimum resource wastage. The quarrying was done in line with the government regulations, guidelines of respective departmental regulatory authorities and international industry standards.
2. Ensuring The Look
The choice of the stone blocks was done as per control samples. The mining was carried out from pred-identified pits/walls to minimize the scope of natural variations. These include consistency in colour and uniformity in the texture of the final product.
3. Precise Cutting
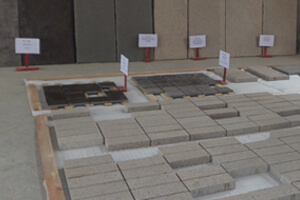
At the production site, the huge blocks were cut into smaller stone slabs of precise thickness. Thanks to our fully automatic block processing machines including gang saw and multi cutter. The results were achieved with stringent accuracy norms for zero variation and zero-defect in stone surfaces.
4. Finishing
The right finish on the stone surface not just enhances its beautiful look but also its functionality. Quality Marble Exports (India) employed state-of-the-art automatic machines for the fast production of world-class finishes as per the highest international standards. Each finish was flawless in every way for minimum rejection at the final quality control point.
5. Cut To Size
The cuts given to each marble flooring tile, for instance, hugely contribute to the design aesthetics of a space. Using Laser Guided Bridge Cutting machines, perfect 90-degree cuts were achieved with zero diagonal variation. 100% accuracy of the process ensured nil tolerance butt joint system at final installation.
6. Final Touch
To produce complicated designs including floral and geometrical patterns, CNC-Waterjet Machines were employed. This ensured high-end final finishing to ease out any rough edges or finishes.
7. Different Approach For Different Products
The dimensions of stones made for interiors such as granite floor tiles are different from the ones used in the exteriors. For the outdoor landscape, extra-thick stones are required. These include cobbles, kerbs, and pavers. These stones were fabricated on specially designed cutting machines for accurate and fast production of desired dimensions. Also, considering the outdoor conditions, the stones were made slip-resistant and frost resistant.
8. Waterproofing/Sealing
Waterproofing is a process that involves extracting the internal moisture from the stone and making it resistant to atmospheric moisture. We applied waterproofing to the required stone. Only our trained and skilled waterproofing agents performed the operation using the latest techniques and chemicals from industry-leading manufacturers.
9. Quality Control At Every Point
Our experienced supervisory staff conducted strict quality control at every point of production. Right from sorting to assessing each piece and rejecting the ones that do not meet the highest standards. Throughout the process of entry and exit of materials in every machine, the materials were examined for quality.
10. Packaging & Unloading
When the final product was ready, packaging was carried out in the most responsible manner. High-quality pest-free, disease-free, clean fresh wood with foam lining, styrofoam sheets were used. Each packaged product was clearly marked as per customer-specified instructions. It assured zero breakage during transit and unloading at the destination.
11. Post-production Service
Quality Marble Exports (India) provided complete service from documentation, production to logistics. Our diligent customer care department worked in coordination to ensure a hassle-free experience in the guarantee of satisfaction at every stage.
Quality Marble Exports (India) - A Leading Manufacturer And Supplier Of Marble, Granite, And Other Natural Stones
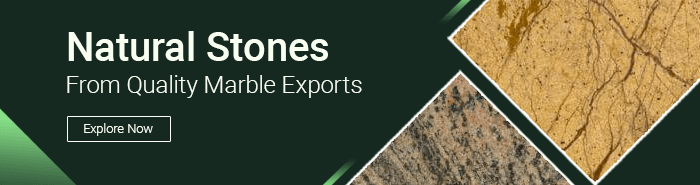
As a leader in the marble and granite suppliers industry, we at Quality Marble Exports (India) are constantly making strides in new manufacturing processes. We work closely with our industrial and manufacturing clients to source aggregates that perform best with our processes. When it comes to quality, we are at the forefront of delivering the best to our customers.
The inspection journey mentioned above is of the project that was accomplished in 2018. Hence, it does not include any post-COVID measures that we apply today for the safety and health of our workers and customers.
From quarrying to installation, Quality Marble Exports (India) ensures high-end processing and service. For all-natural stone products, we offer constant internal and external quality inspection and assurance following the highest industry standards. Our professional team performs quality control inspections on-site. And our geotechnical engineers make sure the product with the highest quality possible reaches our customers.