Artificial stone is increasingly being used in making kitchen countertops and bathroom countertops. The man-made stone is preferred over the natural version majorly due to low prices. However, little does the consumer population know that manufacturing, finishing and installing artificial stones have an adverse health impact on the workers.
Artificial stone contains 93% silica as mineral quartz that produces high concentrations of silica dust during the fabrication process. Studies have found that workers exposed to silica dust are at high risk of developing an irreversible lung disease called ‘silicosis.’ In fact, cases of death caused by silicosis in artificial-stone workers have also been recorded in the US.
Silicosis results from silica dust particles trapped in the lung tissue. This leads to inflammation, scarring and reduced capacity of the lungs to take in oxygen. Also referred to as airborne crystalline silica, the dust increases the risk of lung cancer, chronic obstructive pulmonary disease and kidney disease.
Jose Martinez, a 37-year old man from the US worked years cutting and polishing artificial stone countertops. While at the workshop, the silica dust would be everywhere. On the body, on the clothes, on the tables, on the floor and even in the bathroom. Today, he has developed silicosis. He suffers chest pain, feels weak and dizzy. According to the doctors, the disease is progressive and the only solution is a lung transplant. Two workers (in their 30s) from the same company died due to silicosis the previous year.
The case of Martinez is just one among the 18 cases of illness reported in the US of those primarily involved in fabricating artificial stone. Likewise, 250 cases of silicosis in people working for artificial stone manufacturing were recorded in Australia. Similar outbreaks were also detected in Israel, Italy and Spain.
Measures To Control Silica Dust Exposure
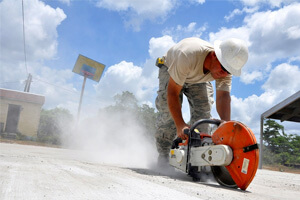
The post-installation product made out of artificial stone is not harmful to the consumers. Only workers involved in dust-generating operations like cutting, grinding, edging and contouring stone are affected. Exposure to silica dust may also come from certain other tasks. These include opening bags of ground quartz, moving or mixing raw materials, and cleaning the dust-laden workshops.
Evidently, workers operating powered hand tools are at the highest risk of exposure to silica dust. Some of these tools are saws, grinders and high-speed polishers.
Therefore, it is crucial that artificial stone manufacturers take stringent measures in controlling the silica dust. The need is to implement a combination of engineering controls, protective equipment, employee training among other measures. A clean and safe working environment ensures the good health of the employees.
Workers involved in dust-generating operations should use personal protective equipment, where appropriate. Proper ventilation systems along with water sprays can ensure cleaner air to breathe.
The floors can be kept clean by using machine scrubs and vacuums. New air handling systems have been observed to bringing silica concentration in the air down to undetectable levels.
Dry Vs Wet Process
As per the research, dry methods of cutting and grinding result in the increased levels of silica in the air. Whereas, the wet process reduces the airborne concentration significantly. That said, the use of contour blades in the wet process is responsible for the highest levels of dust generation.
The lowest levels of silica were observed when computerised and mechanised processing methods were implemented during the wet process. Therefore, it is recommended that stone manufacturers use the latest technology and advanced equipment to shape the final products - right from quarrying.
Precautionary Measures
Workers involved in artificial stone manufacturing for more than three years must undergo a high-resolution CT scan. This will keep a check on the lung health or any kind of lung damage due to exposure to silica. People involved in dry processing for more than a year must also go through the diagnosis.
Quantitative biometric monitoring of functional and inflammatory parameters was used in determining artificial-stone worker exposure to silica in Israel. The findings showed that biometric parameters are helpful for monitoring worker exposure to airborne silica to prevent deterioration over time.
Last but not least, it is also recommended that pre-installation operations should be carried out off-site as much as possible. Implementing a wet procedure, working in controlled operating conditions or performing operations outdoors are three of the sustainable options.
Natural Stone Is Better Than Artificial Stone
The composition of silica is significantly lower in natural stones compared to engineered stones. Granite comprises less than 45% of silica while marble contains less than 10% of it. Calcium-based natural stones such as limestone and certain varieties of marble (onyx, dolomite, calcite) contain negligible to 0% of silica.
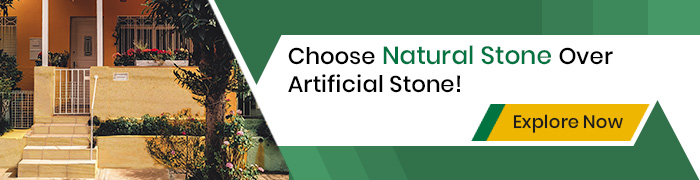
Occupational Safety and Health Administration (OSHA) agency in the US collected air samples from granite and marble workshops. In the marble shop, very low content of airborne silica was detected during the dry grinding process. Even though no engineering controls like water sprays were used, the levels were 39 and 45 µg/m3 - under the safety limits.
In the granite shop, the exposure to silica dust was relatively higher, provided there were no engineering controls implemented. The silica levels ranged from 89 to 460 µg/m3.
Therefore, it is reasonably proven that natural stone workers are at very low risk compared to artificial stones. Even better, a combination of measures implemented in a natural stone manufacturing workshop provides the most healthful occupational conditions to stonemasons.
How Quality Marble Exports (India) Provides The Best Work Environment?
Quality Marble Exports (India) is the leading manufacturer and exporter of natural stones in the country. We supply premium quality natural stone and also ensures healthy working conditions for our skilled workers and craftsmen. Right from the process of quarrying to installing natural stone products, we implement state-of-the-art technology. This not only yields premium quality products but also protects our skilled men from hazardous exposures. Besides, our techniques ensure optimum efficiency and effectiveness at every level of fabrication.
Are you planning a stone installation in your home? Call us for a sustainable yet affordable deal - aesthetics are not ignored! We are the top natural stone suppliers from India.